Unlocking the Power of Welding WPS: Strategies for Efficiency and Safety in Fabrication
In the world of manufacture, Welding Treatment Requirements (WPS) stand as the foundation of welding procedures, dictating the required steps for achieving both efficiency and safety and security in the manufacture procedure. Recognizing the ins and outs of WPS is vital to utilizing its full potential, yet many companies have a hard time to unlock real power that lies within these records (welding WPS). By diving into the techniques that optimize welding WPS, a globe of improved efficiency and heightened safety and security waits for those happy to explore the subtleties of this crucial element of fabrication

Value of Welding WPS
The significance of Welding Treatment Requirements (WPS) in the construction industry can not be overemphasized. WPS work as a vital roadmap that lays out the needed steps to ensure welds are done consistently and correctly. By specifying vital parameters such as welding procedures, materials, joint layouts, preheat temperatures, interpass temperature levels, filler metals, and post-weld warmth treatment needs, WPS supply a standardized technique to welding that enhances performance, quality, and safety and security in manufacture procedures.
Adherence to WPS helps in accomplishing harmony in weld high quality, lowering the possibility of issues or structural failings. This standardization also promotes compliance with market regulations and codes, making sure that made structures satisfy the required security criteria. Moreover, WPS paperwork makes it possible for welders to replicate effective welding treatments, leading to constant outcomes across different jobs.
Fundamentally, the precise advancement and rigorous adherence to Welding Procedure Specs are vital for upholding the integrity of welded frameworks, guarding against prospective threats, and upholding the credibility of manufacture firms for delivering top quality product or services.
Crucial Element of Welding WPS
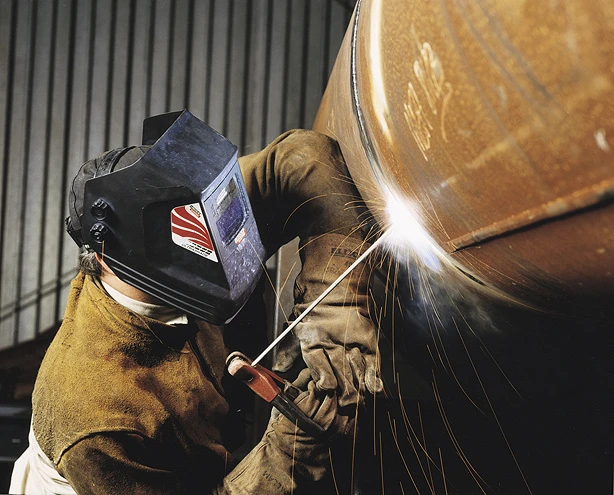
Enhancing Efficiency With WPS
When maximizing welding procedures, leveraging the crucial elements described in Welding Procedure Specs (WPS) ends up being crucial for optimizing and simplifying procedures performance. One means to boost performance with WPS is by meticulously picking the ideal welding criteria. By adhering to the certain standards offered in the WPS, welders can make certain that the welding equipment is set up correctly, leading to high-quality and regular welds. In addition, adhering to the pre-approved welding sequences detailed in the WPS can significantly reduce the moment spent on each weld, eventually raising total performance.
On see post a regular basis reviewing and updating the WPS to integrate any kind of lessons learned or technological innovations can also add to performance improvements in welding operations. By embracing the guidelines established forth in the WPS and constantly looking for ways to optimize processes, producers can attain greater efficiency levels and exceptional end outcomes.
Ensuring Safety And Security in Manufacture
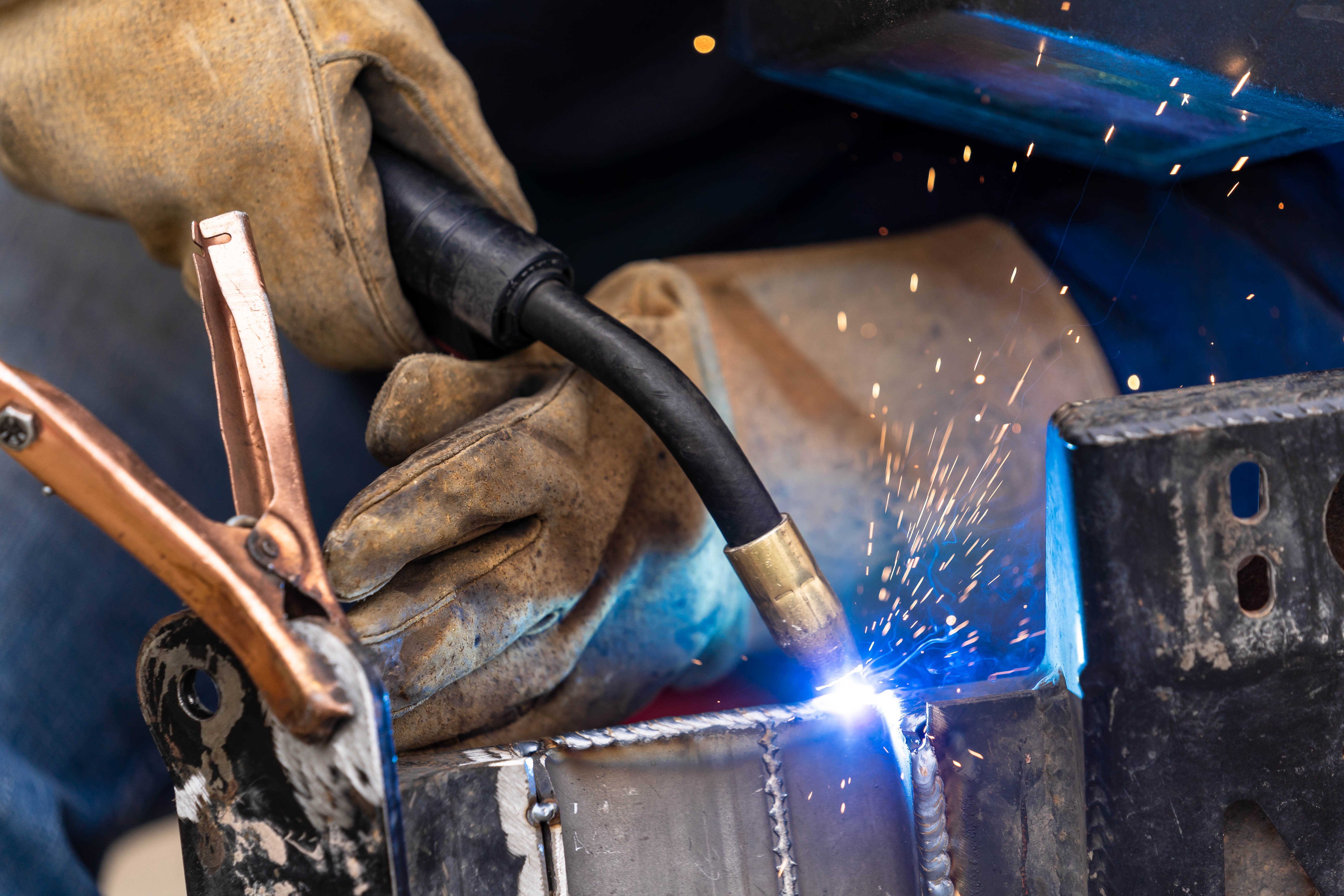
Security protocols in fabrication play a pivotal duty in securing workers and optimizing operational treatments. Making sure security in fabrication entails a complex method that encompasses numerous facets of the welding process. One fundamental facet is the arrangement of personal safety devices (PPE) tailored to the details dangers present in the manufacture atmosphere. Welders should be equipped with ideal gear such as headgears, handwear covers, and protective apparel to reduce risks related to welding activities.
Furthermore, adherence to correct ventilation and fume removal systems is vital in keeping a healthy and balanced workplace. Welding fumes consist of unsafe substances that, if breathed in, can present significant health and wellness threats. Executing effective air flow steps aids to minimize exposure to these unsafe fumes, promoting breathing wellness among workers.
Regular equipment maintenance and inspections are additionally crucial for making certain safety in fabrication. Malfunctioning equipment can lead to injuries and mishaps, emphasizing the importance of regular checks and timely repair services. By prioritizing precaution and cultivating a culture of awareness, fabrication facilities can produce a safe and effective workplace for their personnel.
Executing WPS Finest Practices
To improve resource functional performance and ensure quality outcomes in fabrication processes, incorporating Welding Procedure Specification (WPS) best practices is paramount - welding WPS. Implementing WPS best practices entails thorough preparation, adherence to sector criteria, and continual tracking to ensure ideal results. Firstly, selecting the ideal welding procedure, filler product, and preheat temperature specified in the WPS is essential for achieving the wanted weld top quality. Second of all, making sure that qualified welders with the necessary qualifications perform the welding treatments according to the WPS guidelines is important for consistency and reliability. On a regular basis upgrading and evaluating WPS documents to mirror any type of process improvements or adjustments in materials is also a vital finest practice to keep accuracy and relevance. In addition, offering comprehensive training to welding employees on WPS demands and best methods fosters a society of safety and security and top quality within the construction environment. By diligently applying WPS finest practices, producers can streamline their procedures, minimize mistakes, and deliver remarkable products to fulfill client assumptions.
Verdict
To conclude, welding WPS plays an important duty in ensuring effectiveness and safety and security in manufacture processes. By concentrating on crucial elements, enhancing efficiency, and executing ideal techniques, companies can optimize their welding operations. It is vital to focus on precaution to avoid mishaps and make sure a smooth manufacturing procedure. By adhering to these strategies, companies can unlock the full capacity of welding WPS in their construction procedures.
In the world of manufacture, Welding Treatment Specs (WPS) stand as the backbone of welding operations, dictating the necessary steps for attaining both performance and safety and security in the manufacture process. By specifying essential click to find out more criteria such as welding processes, products, joint styles, preheat temperatures, interpass temperatures, filler metals, and post-weld warmth therapy demands, WPS offer a standardized approach to welding that boosts performance, high quality, and security in fabrication procedures.

When optimizing welding operations, leveraging the crucial components described in Welding Treatment Requirements (WPS) becomes necessary for making the most of and enhancing procedures performance. (welding WPS)